James Roberts is a Field Safety Skills Specialist at Shell’s Deer Park Manufacturing Complex. Recently he was challenged to onboard the site’s turnaround contract partners in a new and engaging way – through Visual Onboarding. This is what he has to say about it:
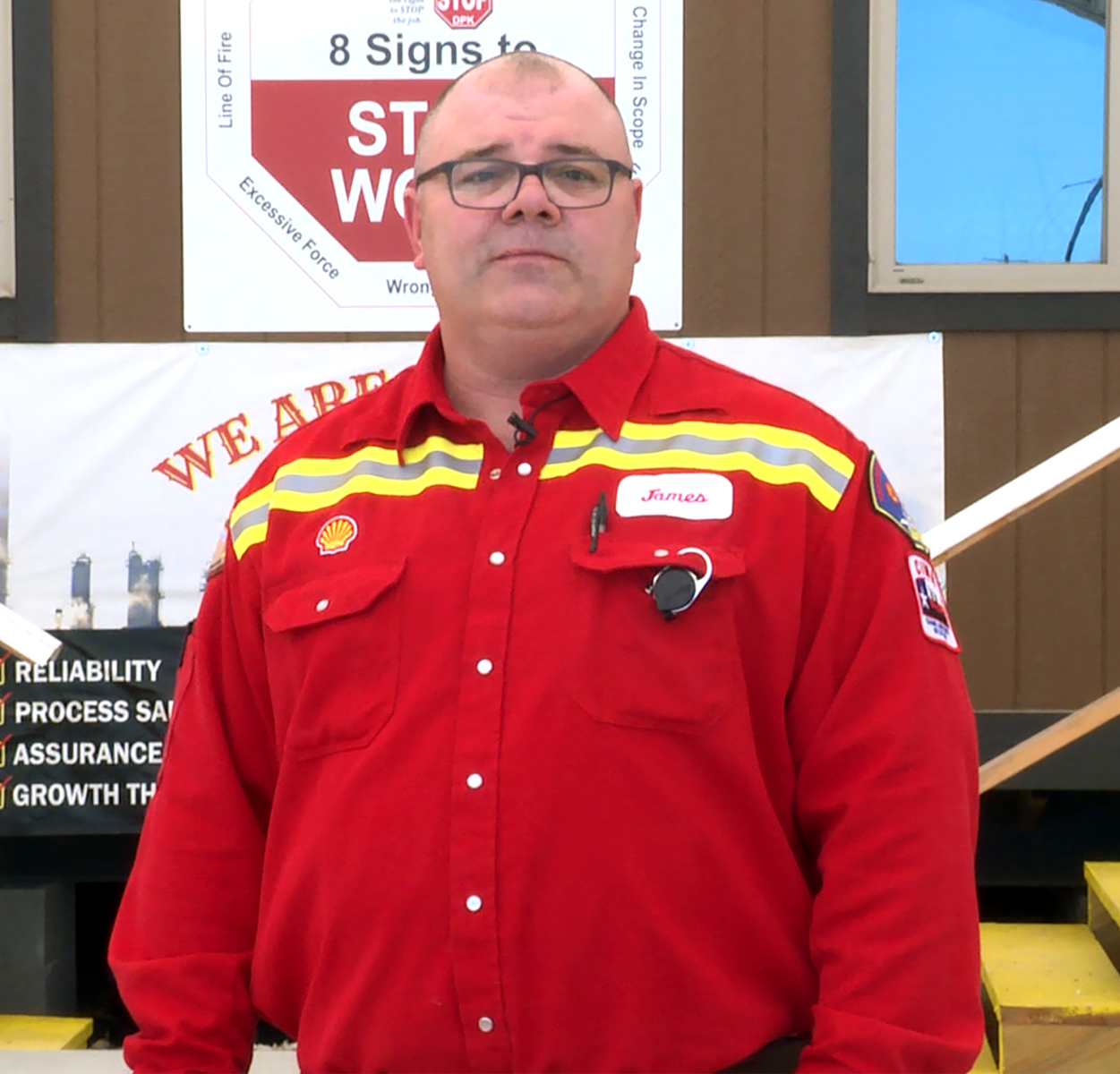
First off, let’s talk about what a turnaround really is which is a regular maintenance that happens every 4-6 years on a given piece of equipment. It’s similar to maintenance we perform to keep our vehicles running properly.
During an industrial turnaround, equipment is shut down, inspected, repaired or replaced, and cleaned to ensure safe and reliable operations for years to come. It is also an opportunity for us to make capital investments to improve process safety, reliability, and leverage new growth opportunities that cannot otherwise be completed during normal operations.
In preparation for the joining contract workforce, the Health and Safety team set up a Visual Onboarding Center to personally onboard each contractor to our safety culture. Focusing on how to quickly get people up to speed, without losing sight of hazards and our processes, the Visual Onboarding Center consists of 10 booths showcasing the most common work scenarios that occur during a turnaround and highlight the stop-work authority that all workers have at our site. These scenarios or cases-for-action ensure onboarded workers understand critical information that they can then apply in the field. What makes this resource so powerful is the personal connection it provides – taking the safety learning experience from one-way communication to two-way conversations.